Three Reasons Why Factory Workers Should Stop Clocking in Manually
For decades, the manufacturing industry has been using traditional processes such as clocking in and clocking out. Factory workers manually ‘check in’ using physical time sheets after arriving at the warehouse, and ‘check out’ once their shift is over.
But, things have to change.
In this day and age, optimizing processes and gaining efficiency are key. This is especially true for manufacturing – an industry that consists of 80% of the non-desk global workforce. In fact, digitalization is rapidly spreading across all manufacturing functions, from the back office all the way to the production floor. Companies are on the fast track to optimizing their processes using technology…and HR processes are no exception.
Are your factory workers still manually clocking in? Here are the many reasons not to.
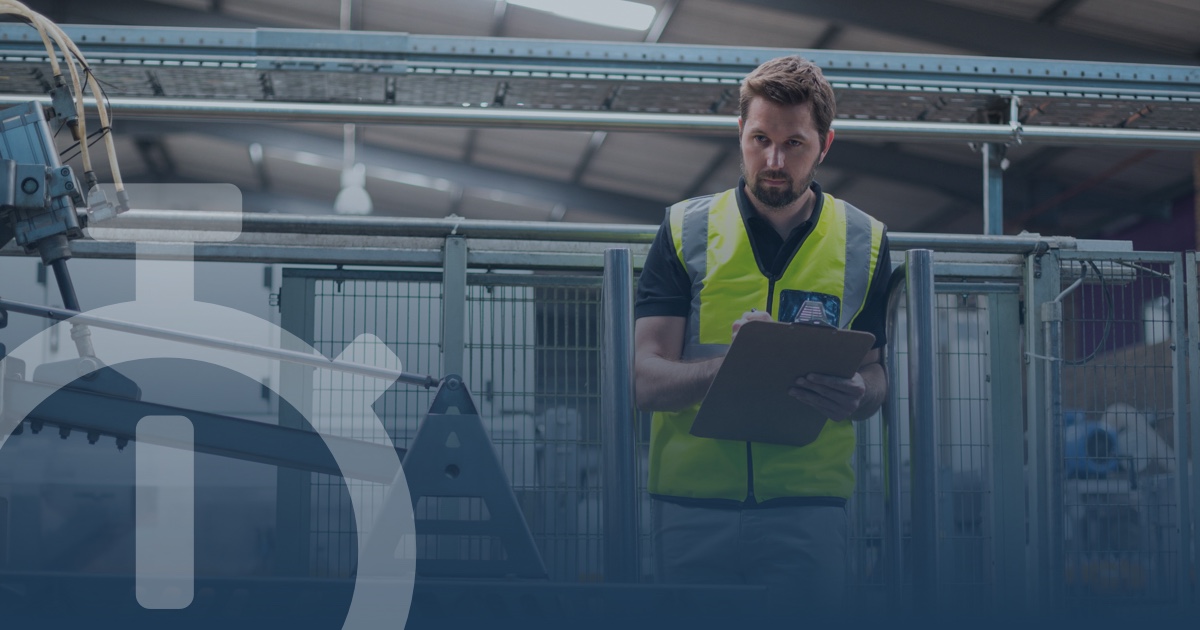
Factory workers need important information before their shifts start
That’s right! A recent report by Deloitte showed that 49% of factory workers waste an average of 3 hours per week due to a lack of tech devices. And that’s simply because floor workers don’t have the right information they need to do their job. That’s demotivating (and soul-crushing) and automatically decreases employee engagement.
At this point, you can imagine those factory workers who start their shifts with missing information need to spend an extra amount of time hunting down that other person on the production floor who knows the answer. And with traditional processes, it’s challenging to share information, making it harder to scale and onboard new manufacturing employees.
But with digital tools, such as an employee app, factory workers are able to read company information before their shifts start, receive all the details they need, and ask about any uncertainties they may have. More and more manufacturers are seeing the benefits of mobile-friendly digital workplaces, and are making sure that employees have all the information they need. What’s more, employees can use the employee app to exchange best practices with other floor workers (at any branch) and receive guidance.
Here’s the cherry on top: McKinsey found that employee productivity increases 20-25% in organizations where employees are highly connected. Trust the data folks.
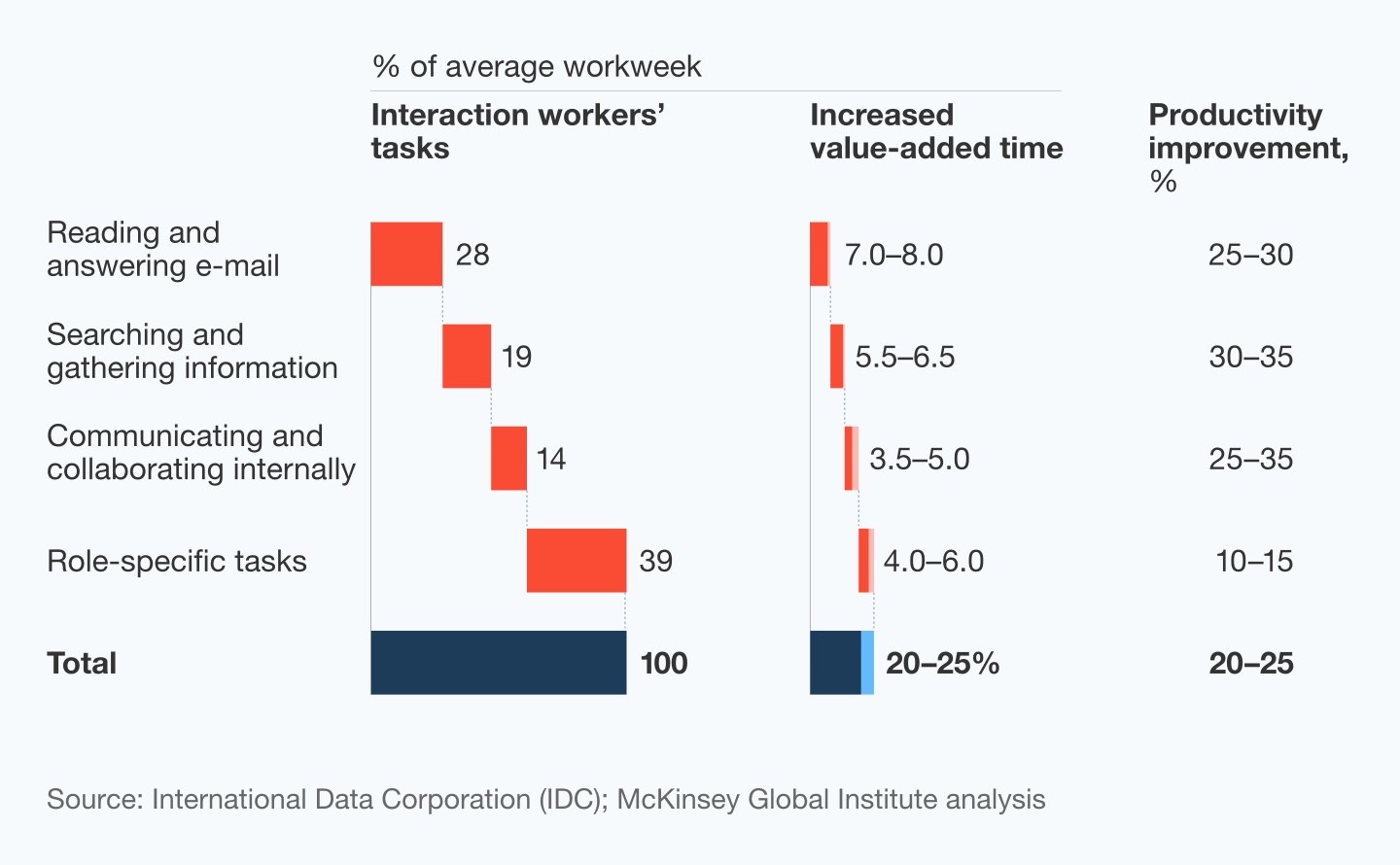
Factory workers are already online; meet them there
It’s important to modernize your HR systems in order to keep up with employees’ expectations and needs. The younger generation joining the workforce is used to communicating in a certain way, and you need to engage those factory workers in a familiar space. In fact, only 10% of deskless workers feel strongly connected to their companies. As a result, this drives them towards technology that they use in their personal lives, such as WhatsApp, to find their co-workers and fill the gaps.
Let’s face it, announcements on bulletin boards and manual clock-ins in the manufacturing industry are a thing of the past. It worked for decades, but technology has found solutions to increase production and productivity, as well as employee engagement. Your factory workers are already online; they’re using their mobile phones for leisure, so why not meet them where it’s familiar using an employee app? That’s right, no more manual clock-ins, and instead a place they can receive all the information they need, in real-time too. Let them swap shifts, check their schedules, find tasks, exchange best practices with co-workers, and get the answers they need.
{{cta('0caee6f5-e10f-4ef0-a079-c77500a9b830','justifycenter')}}
Manage shifts efficiently with an employee app
At first glance, it may seem financially unreasonable to implement employee digital tools (such as an employee app) in manufacturing, but a deep dive into this issue tells us quite the opposite.
Truth is, there’s no effective way to reschedule shifts with manual (or paper) time sheets. Time spent on the production floor is valuable and can cost the company a ton of money if mismanaged. So when a manufacturing employee doesn’t show up for their shift, that’s a big gap that needs to be filled instantly. But how can a production supervisor keep track, or even reach out for a replacement? It creates an obstacle and one that needs to be dealt with on the spot.
After interviewing some of our customers in the manufacturing industry, we’ve learned that floor workers were the most excited ones to make the switch to an employee app that integrates with online scheduling. Why is that? With digital tools, manufacturing employees can see their schedules, as well as plan and swap shifts in real-time. That also keeps the production supervisor in the loop about what to expect on the production floor, and avoids the hassle of reaching out to other employees for a replacement. Planning is simple, and it’s an employee app that anyone can use (without an email address).
What’s more, vacation days can be requested and approved using the employee app, making it easier for floor workers and production supervisors to keep track of schedules and shifts.
{{cta('d377818e-6d5e-4954-967f-5a97a8aa2e72','justifycenter')}}
Three Reasons Why Factory Workers Should Stop Clocking in Manually
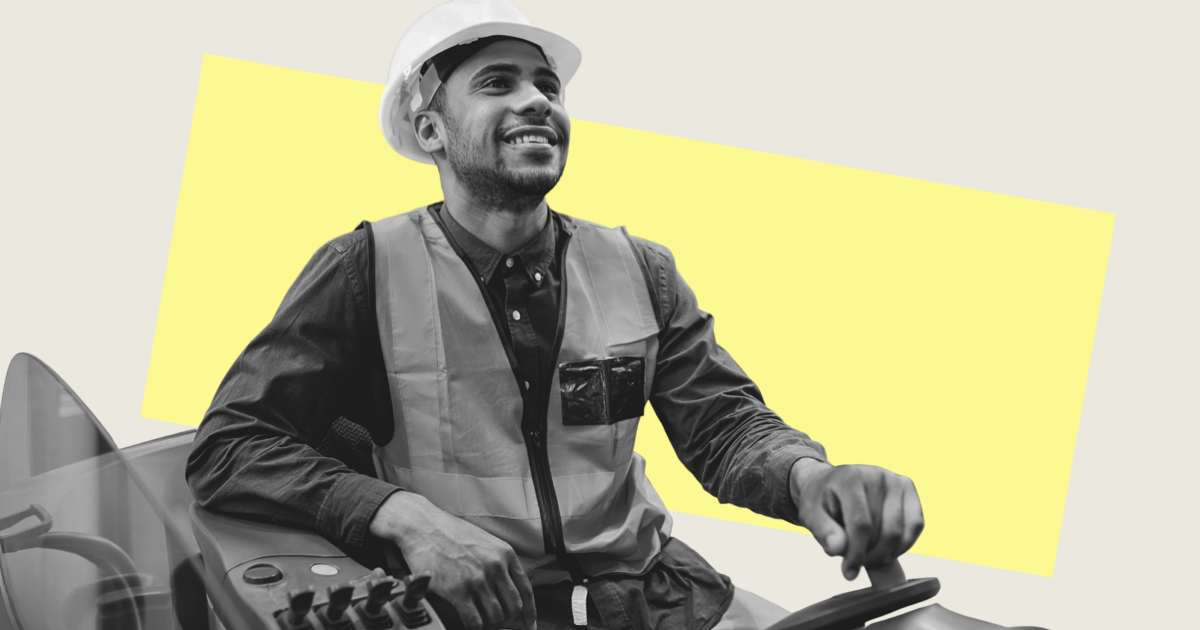
For decades, the manufacturing industry has been using traditional processes such as clocking in and clocking out. Factory workers manually ‘check in’ using physical time sheets after arriving at the warehouse, and ‘check out’ once their shift is over.
But, things have to change.
In this day and age, optimizing processes and gaining efficiency are key. This is especially true for manufacturing – an industry that consists of 80% of the non-desk global workforce. In fact, digitalization is rapidly spreading across all manufacturing functions, from the back office all the way to the production floor. Companies are on the fast track to optimizing their processes using technology…and HR processes are no exception.
Are your factory workers still manually clocking in? Here are the many reasons not to.
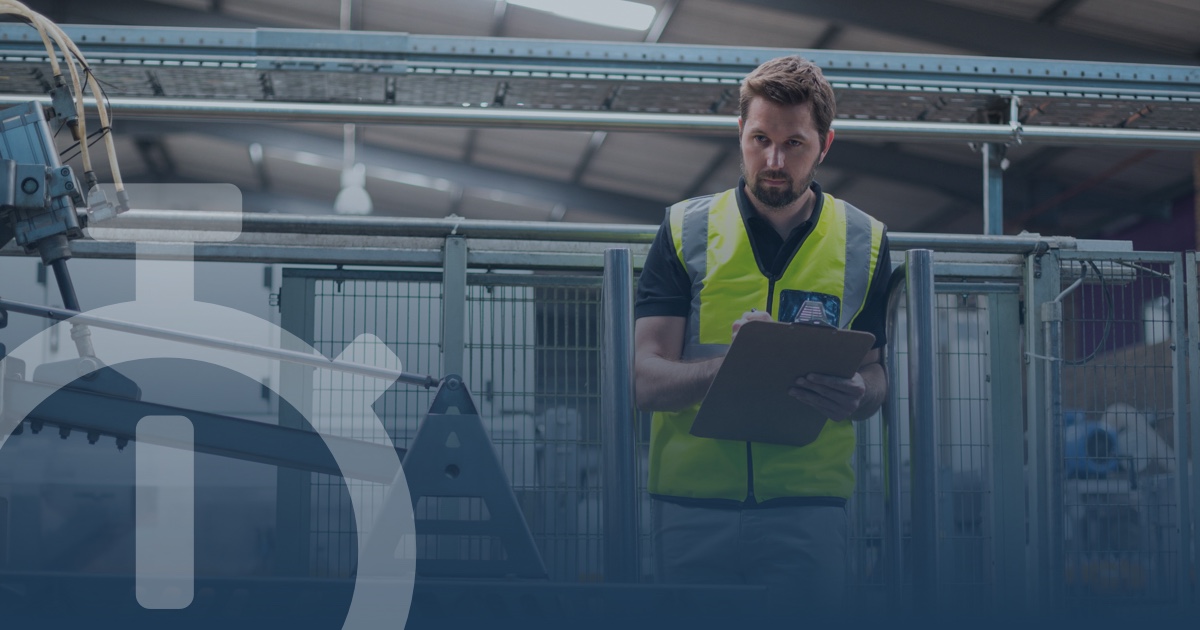
Factory workers need important information before their shifts start
That’s right! A recent report by Deloitte showed that 49% of factory workers waste an average of 3 hours per week due to a lack of tech devices. And that’s simply because floor workers don’t have the right information they need to do their job. That’s demotivating (and soul-crushing) and automatically decreases employee engagement.
At this point, you can imagine those factory workers who start their shifts with missing information need to spend an extra amount of time hunting down that other person on the production floor who knows the answer. And with traditional processes, it’s challenging to share information, making it harder to scale and onboard new manufacturing employees.
But with digital tools, such as an employee app, factory workers are able to read company information before their shifts start, receive all the details they need, and ask about any uncertainties they may have. More and more manufacturers are seeing the benefits of mobile-friendly digital workplaces, and are making sure that employees have all the information they need. What’s more, employees can use the employee app to exchange best practices with other floor workers (at any branch) and receive guidance.
Here’s the cherry on top: McKinsey found that employee productivity increases 20-25% in organizations where employees are highly connected. Trust the data folks.
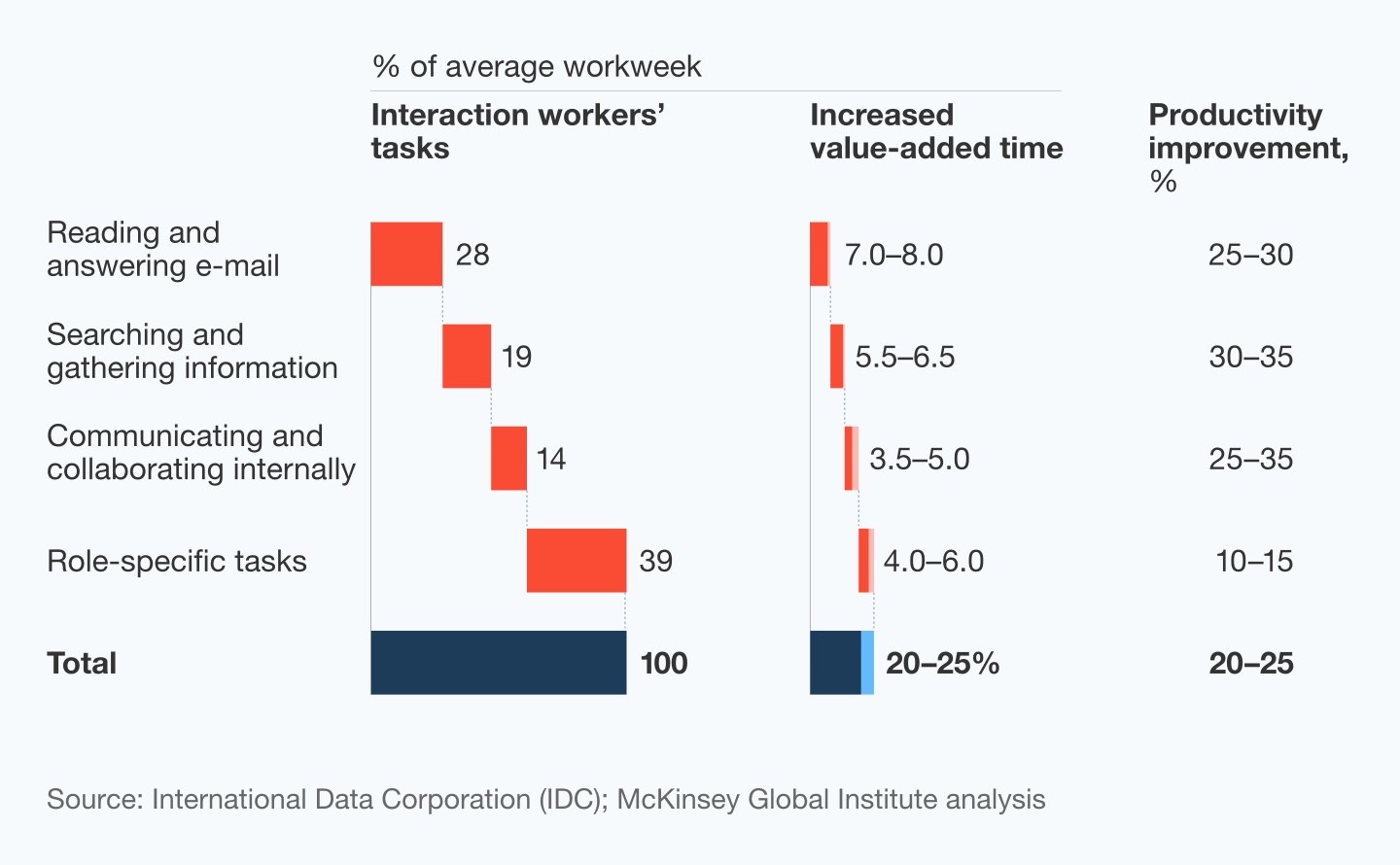
Factory workers are already online; meet them there
It’s important to modernize your HR systems in order to keep up with employees’ expectations and needs. The younger generation joining the workforce is used to communicating in a certain way, and you need to engage those factory workers in a familiar space. In fact, only 10% of deskless workers feel strongly connected to their companies. As a result, this drives them towards technology that they use in their personal lives, such as WhatsApp, to find their co-workers and fill the gaps.
Let’s face it, announcements on bulletin boards and manual clock-ins in the manufacturing industry are a thing of the past. It worked for decades, but technology has found solutions to increase production and productivity, as well as employee engagement. Your factory workers are already online; they’re using their mobile phones for leisure, so why not meet them where it’s familiar using an employee app? That’s right, no more manual clock-ins, and instead a place they can receive all the information they need, in real-time too. Let them swap shifts, check their schedules, find tasks, exchange best practices with co-workers, and get the answers they need.
{{cta('0caee6f5-e10f-4ef0-a079-c77500a9b830','justifycenter')}}
Manage shifts efficiently with an employee app
At first glance, it may seem financially unreasonable to implement employee digital tools (such as an employee app) in manufacturing, but a deep dive into this issue tells us quite the opposite.
Truth is, there’s no effective way to reschedule shifts with manual (or paper) time sheets. Time spent on the production floor is valuable and can cost the company a ton of money if mismanaged. So when a manufacturing employee doesn’t show up for their shift, that’s a big gap that needs to be filled instantly. But how can a production supervisor keep track, or even reach out for a replacement? It creates an obstacle and one that needs to be dealt with on the spot.
After interviewing some of our customers in the manufacturing industry, we’ve learned that floor workers were the most excited ones to make the switch to an employee app that integrates with online scheduling. Why is that? With digital tools, manufacturing employees can see their schedules, as well as plan and swap shifts in real-time. That also keeps the production supervisor in the loop about what to expect on the production floor, and avoids the hassle of reaching out to other employees for a replacement. Planning is simple, and it’s an employee app that anyone can use (without an email address).
What’s more, vacation days can be requested and approved using the employee app, making it easier for floor workers and production supervisors to keep track of schedules and shifts.
{{cta('d377818e-6d5e-4954-967f-5a97a8aa2e72','justifycenter')}}
Related Articles
Stay updated with the latest insights and trends delivered straight to your inbox.